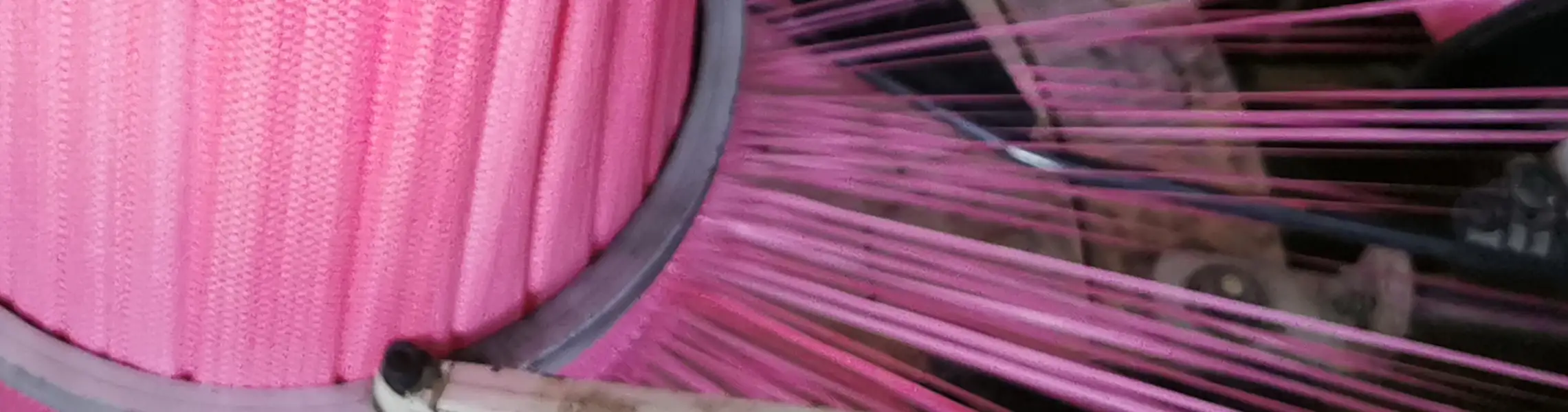
Masterbatches
Masterbatch is a solid additive used for coloring (color masterbatch) or imparting other properties (additive masterbatch) to plastic. Masterbatch is a concentrated mixture of pigments and/or additives which is manufactured by encapsulation during a heat process or twin-screw extrusion into a carrier matrix resin, which is then cooled and further cut into a granular shape. Masterbatch allows the processor to color raw polymer economically.
Benefits
Easy to handle, pollution free, quality consistency, hassle-free production, effortless inventory management.
Applications
Injection molding, blown film, extrusion, cable, roto molding, blow molding, woven sacks/raffia, non-woven.
The white masterbatch is the high-quality pigment that is used on plastics. This kind of masterbatch can be used for lamination, coating, used as a protective film, molding, etc. They contain high quality outdoor and indoor Titanium Dioxide (TiO2) grades, percentage varies from 20% to 70% depends on end application.
In simple language, a black masterbatch comprises a high concentration of carbon black. Its volume ranges between 15-50%. It is dispersed in thermoplastic resins. Here, the thermoplastic resin acts as a carrier. It is also called a binder. Generally, black masterbatches comprise up to 50% of carbon black content in their composition. As a result, it is tailor-made to function as a black pigment in a wide range of plastic applications.
Benefits include high jets, UV stability, uniform dispersion, resistant to high temperature, no issues of bleed or bloom, and simple to process.
A color masterbatch, or color concentrate, is a granule used for coloring thermoplastics. It consists of one or more colorants and a polymer-specific carrier resin. The composition of a color masterbatch is called its recipe. Colorants are classified into several categories: organic dyes, organic pigments and inorganic pigments. Dyes are soluble in plastics and can therefore be used for transparent coloration. Pigments remain in their original particle form inside the plastic and need to be dispersed within the plastic. The recipe for a specific color masterbatch is developed in laboratory based on a customer’s requirements. A color masterbatch may contain up to 60% colorant. In the subsequent production process, the colorant is introduced into the melted plastic.
Additives are chemicals added to the base polymer to improve processability, prolong the life span, and/or achieve the desired physical or chemical properties in the final product. While the content of additives is typically only a few percent, their impact on polymer performance and stability is significant.
Types of Additive Masterbatches
Antioxidant | Inhibits degradation caused by thermo-mechanical or thermo-oxidative conditions |
Antistatic | Protecting Plastic from The Burden of Static Electricity |
Antiblock | To prevent film sheets to stick together |
Antimirobial | To inhibit growth of microbes |
Antifog | To prevent condensation of water vapor on the surface of a clear plastic film |
Slip | To reduce friction between polymers and processing equipment and between polymer-to-polymer interfaces |
Desiccant | To eliminate humidity/remove moisture |
Fragrance | Adding fragrance MB masks the unpleasant odour & releases it with the desired aroma. |
UV | Protects the polymers against UV-degradation, avoid discoloration and improves the processibility |
Polymer Processing | Concentrate designed to enhance the extrusion of various thermoplastic resins, by improving process efficiency, product quality and machine throughputs |
Optical Brightener | To reduce yellowing, improved whiteness, and to enhance the brightness of a product. |